Vibration Testing
Vibration testing covers a wide rage of testing methodologies, instrumentation, and analysis techniques. The links under System Vibration cover many of them. Vibration testing can be grouped into two areas Vibration Characterization and Dynamic Testing.

Semiconductor Inspection Tool Testing Using Sub-Nanometer Capacitive Sensor Between Wafer and Optics Plate
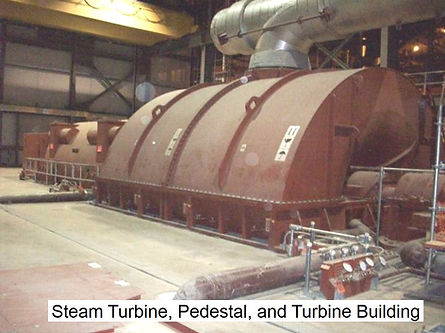
120 Megawatt Steam Turbine, Concrete Turbine Pedestal, and Steel Building Structure, Using Thermal Analysis and Operating Deflection Shape Testing (ODS)
Our approach - We most often characterize a problem first and work from known conditions, and stay in “the known” as we proceed by making sense of what we observe as we move forward. We test and analyze the change in dynamics we are trying to create in real-time, on site, and often make changes to our experimental test plan on the fly as we discover how a system is actually behaving. In doing so we often get meaningful results from which we can make sound engineering decisions in a short time frame. We don't just make measurements and spit out data. We help identify the problem and propose solutions.
​
We have developed and refined measurement techniques to sort out acoustically driven vibration, environmental vibration, and internal vibration sources. These tests and analyses are used to show how the dynamics of a structure and the surrounding environment couple to provide the transmission of vibration from these various sources to the critical components of the system.
When we first consider a vibration issue we most often start with a characterization of a disturbance response that is thought to be associated with the vibration problem at hand. This initial characterization testing is critical to pointing the engineering team in the right direction and quantifying the problem. It provides a larger picture that allows a set of informed hypotheses to be put forward that will drive further dynamic testing and analysis, and lead to a set of effective options to mitigate or eliminate the vibration problem.
The measurements of the disturbance response may include relative displacement between two critical parts, absolute acceleration, velocity, or displacement at a set of locations on the system, stress, strain, temperature, flow, etc.
We analyze data in both the time and frequency domains using various analysis techniques. Our decades of experience as experts in this unique field allow us to propose an experimental design that will hone in on the heart of the issue quickly and efficiently with the right instrumentation selection, bandwidth, mounting techniques, and digital processing considerations.
​
Questions that will often be asked after an initial Vibration Characterization are:
-
Is the disturbance response due to excessive force levels from one or more sources of excitation?
-
Is the disturbance response due to quite reasonable excitation levels that are being amplified by unexpected resonant amplification of the system, or both?
-
If it is a resonance problem, what is creating this resonance?
-
How does the system deform as it vibrates to create the resonant mode and the unwanted vibration response?
-
If the vibration issue is due to unwanted levels of excitation disturbance how does one identify the source(s) and locate them?
​
Dynamic Testing
Most everyone will tap on an object to determine what it is made of, if it's broken and cracked, if it's hollow or solid, if its full or half full, hard and resilient, or soft and damped, just by the feel and the resulting sound. Dynamic testing is simply a highly advanced extension of this basic human investigative impulse.
​
Determining Cause & Effect
​
How do we explain the vibration response we observe? We use dynamic testing to quantify structural amplification, identify transmission paths, and gather data that can be used to identify the critical resonances and the corresponding mode shapes of a structure. We can estimate the input force levels that must be acting on a structure to explain the measured response during operation. Dynamic testing is the basis of vibration analysis and Modal Analysis testing, and a powerful tool in identifying cause and effect in our Diagnostic Testing.
​
In working with an engineering team to find solution options, dynamic testing can tell us:
-
Where on the structure added stiffness will have a benefit, and where it will not.
-
Where will a damping treatment be effective and where it will do nothing.
-
What changes to the mass distribution will be effective, and where changes can make things worse.
-
How the resonances of a system, and their corresponding mode shapes, determine the vibration and acoustic sensitivities of a system.
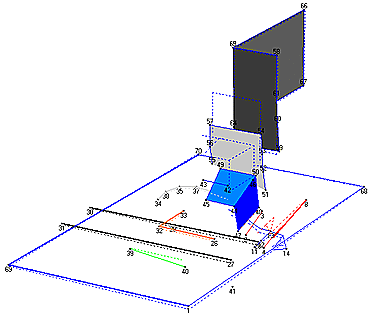
AFM Modal Analysis Mode #5 at 72 Hz
Excited by Cooling Fan
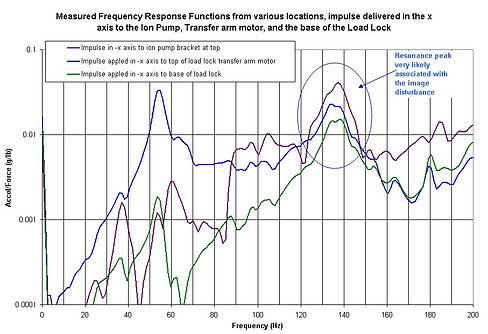
FRF showing Resonance ID in Scanning Electron Microscope Image Disturbance Issue
Many engineers will recall that the peaks in an FFT of a vibration response to an impulse, or swept-sine input, often correspond to the resonances of the structure. This is a very valuable concept that helps predict at what excitation frequencies we should expect large motions. What most people don’t think about as often is what the deformation shape looks like as the system oscillates at resonance? We spend much of our time thinking about just that.
The fascinating thing about these resonances is that each resonant peak corresponds to a unique deformed shape called a mode shape. In other words, a mode shape is the unique deformed shape a structure will take as it oscillates at a unique resonant frequency. The resonant frequency and mode shape are collectively referred to as a mode. Understanding the mode shape allows the structural dynamics to be accessible to the engineering team and provides a unique visualization of the vibration problem that is tangible. We often hear a collective "Ahh Ha!" when presenting animated representations of our Modal Analysis results.
​
​​Frequency Response Function (FRF) - The FRF involves measurement of both the response and the input force. The FRF is a measurement of the response at a given point on a structure, per unit input force at another point as a function of frequency. The ratio of the response to the input force as a function of frequency is called the Transfer Function, or the Frequency Response Function (FRF). The resonant parameters can be extracted numerically from these FRFs and include the resonant frequencies, the local stiffness, mass, and damping. Measurement of the frequency response function (FRF) is our most powerful tool. It contains the “fingerprint” of the inherent structural dynamics of a system.
​
We often perform a vibration characterization along with dynamic tests (Force & Response measurements) to determine the structural dynamics that influence resonant amplification and transmission from the disturbance sources to the critical structures. We use our estimates of the dynamic parameters to suggest structural modifications, and often create optimized custom Damping Treatment Designs.
​
Measurement of the frequency response function (FRF) is our most powerful tool. It contains the “fingerprint” of the inherent structural dynamics of a system.
​

Structural modifications to improve the stiffness of an optical structure, the torsional resonance is increased by making progressive improvements to the backbone frame structure.
Computer representation of a semiconductor tool used for animation of mode shapes from dynamic testing on the physical system
Dynamic testing and Frequency Response Function (FRF) measurement are used in a systematic way to collect the data for a Modal Analysis which is used to create visualizations of these unique mode shapes. The modes can show how and why these resonances form and what can be done to change them so that the tool will have less sensitivity to environmental disturbance. Change the mode shape and we change the resonance frequency, the input and response relationship, and the product, facility, or tool performance. The modes can be superimposed to approximate the possible deformed motions of the structure. The characterization of a subset of these modes is often all that is necessary to gain a full understanding of the deformations that dominate a vibration and/or acoustic problem. A more detailed discussion of the very powerful concepts of Modal & Resonance Testing are given under that title.
Dynamics Parameters - The resonant parameters can be extracted numerically from these FRFs and include the resonant frequencies, the local stiffness, mass, and damping. We can show the coupling between structures, debug disturbance path issues, and estimate sensitivity to disturbance (which is what an FRF essentially is). The way force and response are measured using digital signal processing allows us to average out external disturbances that are not caused by the measured applied input force. This is a powerful tool for showing cause and effect in the troubleshooting process.
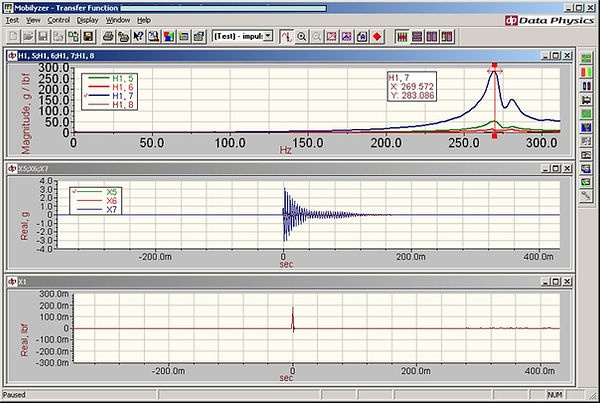
Top trace is the Frequency Response Function (FRF), with a peak at the resonant frequency, relating the response per unit input. The middle trace is the response of the structure ringing down at its resonant frequency, the bottom trace is a measurement of the the input force impulse
Below is a plot showing the frequency response function (top blue trace) measured on a structure on a scanning electron microscope (SEM) that involved many important resonances. These resonances can be seen to dominate the ambient response of the tool (middle green trace). We hit the jackpot with this measurement because this one FRF identified a structure responsible for the amplification of the bulk of the disturbance to this sensitive inspection tool. The ambient environment, however, was relatively flat, both in the floor vibration (purple trace) and in the acoustics noise (red trace), making for a particularly easy "imprint" of the shape of these resonances from the FRF in the ambient spectra (middle green trace). We made a couple hundred such measurements before finding this unique FRF. Often important resonances will be found in a handful of FRF measurements. It may look like colorful wiggly lines on the plot below represent the "Smoking Gun" we were hoping to find.

Overlay of the FRF, showing the resonances of the structure (Blue Trace), the floor vibration spectra (Purple Trace), the System Response dominated by the structural resonances (Green Trace), the acoustic spectrum (Red Trace)
The plot below is a set of FRFs measured on a bio-tech device that originally had very poor image quality due to structural resonances of the sample holder. We used dynamic testing and the FRF to characterize the improvements in resonant behavior for various structural modifications and Damping Treatments, quantifying our analysis, and allowing our client to predict image disturbance for given external excitations, such as environmental chamber vibration. These measurements and calculations can then be used to engineer isolation of sources of the environmental chamber, etc.


Damping Treatments Include Tuned Mass Dampers When Appropriate

Optical Mirror Actively Controlled,
Secondary Resonances Limit Servo Bandwidth
Dynamic testing is the backbone of all of our work, it is the basis of vibration analysis and Modal Analysis Testing, and the way we show cause & effect in our Diagnostic Testing. Most everyone will tap on an object to determine what it is made of, if its broken and cracked, if its hollow or solid, if its full or half full, hard and resilient, or soft and damped, just by the feel and the resulting sound. Dynamic testing is simply a highly advanced extension of this basic human investigative impulse.
As vibration consultants, we work with our client's engineering team to make the vibration problem understandable, providing guidance in experimental design. We select and provide the instrumentation to do testing and analysis to characterize the problem and quantify the important components of the problem. We provide visualization of structural issues and allow the team to optimize practical and engineered solutions, based on valid test data, in a short time frame.




Tools of the Trade, Amplifiers, Filters,
Shakers, Force Sensors, Accelerometers
We have developed and refined measurement techniques to sort out acoustically driven vibration, environmental vibration, and internal vibration sources. We can provide The Big Picture by showing how the dynamics of a structure and the surrounding environment couple to provide the transmission of vibration from these various sources to the critical components of the tool.
We use a wide variety of instrumentation including accelerometers of various sizes and sensitivities each suited for specific purposes. We use geophones and seismographs where needed. We use relative displacement sensors of various kinds including capacitive sensors, and eddy current probes and optical sensors, in a variety of geometries and sensitivities. We understand the idiosyncrasies and limitations of instrumentation that include the frequency response, thermal noise, cross-coupling, electrical noise sensitivity, and linearity. We also know the digital signal processing side of our business.

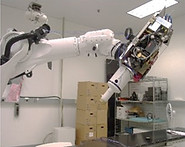
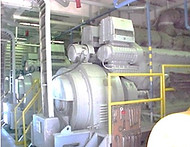
Self-Induced Vibration: Control Instability, Transient Ringdown After Move, Engine Vibration
We have worked on a myriad of systems. From nanometer level disturbances of scanning electron microscopes, to micron level motions of giant mountain-top telescopes, to centimeter level motions of offshore oil rigs. We have worked on hundreds of industrial, biomedical, semiconductor, and commercial systems worldwide to improve performance, and to solve imaging, measurement, vibration and acoustic issues.
We work with architectural teams in the planning of new Facilities, and in repurposing existing facilities, providing guidance in translating vibration and acoustic requirements into design specifications, and taking on unique design challenges. Our work includes projects ranging from semiconductor cleanrooms, laboratories, hospitals, office buildings, and industrial facilities. We provide testing, analysis, of existing sites to quantify the vibration and acoustic parameters needed to properly characterize an existing site. (See our Client list ).
By performing dynamic testing, including measuring the system's vibration response to applied forces (also called frequency response functions or FRFs), we can quickly get a larger picture of the structural dynamics, causes of resonant amplification, and the nature of the disturbance transmission path. With this understanding we can often quickly narrow down on the possible nature and scope of the problem and a solution to the vibration problem can be designed quickly and efficiently.
​
As vibration consultants, we work with our client's engineering team to make the vibration problem understandable, providing guidance in experimental design. We select and provide the instrumentation to do testing and analysis to characterize the problem and quantify the important components of the problem. We provide visualization of structural issues and allow the team to optimize practical and engineered solutions, based on valid test data, in a short time frame.
​
Whether making a few dynamics measurements, or a full modal analysis, we use the concepts relating to FRFs and dynamic and modal analysis testing to develop the understanding of the vibration problem to allow efficient solution development. We have been advancing these structural dynamics vibration problem solving techniques since Response Dynamics was founded by our President, Reuben Hale, PE, 35 years ago. Henry Bittner, MSME, our VP of Engineering, joined our company a few years later, and has been an integral part of our team for over 25 years. During this entire time we have been working extensively, in the field and in our lab, solving a wide range of clients' vibration issues, on a diverse variety of systems and structures including:
​
-
Building floor structures to support critically sensitive systems
-
Electron microscopes
-
Astronomical telescopes
-
Interferometers
-
Gene sequencers and other biomedical research systems
-
Vibratory Conveyor Systems for food and for industrial and mining applications
-
Farm and Construction Grader automatic blade position control systems
-
Paper Plant Machinery and floor systems
-
Photovoltaic solar trackers
-
Power steam turbines
-
Wind turbines
-
Helicopter and jet aircraft (full size and scale model)
-
Flight simulators
-
Semiconductor inspection and fabrication systems and facilities
-
Medical systems ranging from Surgical Robots to Home Dialysis Systems
-
Particle accelerators ranging from Federal Research Facilities to Medical Patient Radiation Therapy Systems
-
Guitars and Guitar strings
-
Hand tools
-
and hundreds of others.
We love what we do and are at the very top of our unique field.